Men’s Health Week 2024 is celebrated between the 10-16 June. This event aims to raise awareness concerning health issues that predominately affect men. The theme for Men’s Health Week 2024 is to support men in taking charge of their well-being, encourage them to make wise lifestyle decisions, and seek medical care when necessary.
Get involved in Men’s Health Week 2024
It’s time to inspire and support the men in your life by encouraging them to participate in any of the following:
- Make an appointment for a health check-up: Make an appointment for a routine check-up with your healthcare provider. Early detection from disease increases recovery rates.
- Sign up to a health education courses: Take part in an educational seminars or workshops that covers issues related to men’s health including mental health related issues.
- Take part in physical activities: During Men’s Health Week, plan sports events or group activities to encourage physical fitness. Improving your overall health as a result.
- Share current health statistics: Increase public knowledge of particular health issues, preventative measures, and accessible resources.
As we focus on supporting men’s health, it’s equally important for employers, especially those with employees working at heights, to ensure rigorous risk assessments are conducted to safeguard their workforce from potential injuries at work.
Protect workers health with an effective safety plan
As required by the Working at Height Regulations of 2005, employers must guarantee the security of their employees by putting safety plans in place that lower the possibility of fatalities or serious injuries from falls and possibly falling objects. However, a risk assessment needs to be completed before said plans can be put into action. This risk assessment considers all reasonable possibilities that could lead to worker injury. Owners of businesses and supervisors can then plan the work based on the risk assessment.
One of the most crucial parts of the whole safety plan is the risk assessment. It is very difficult to put safety plans into action without a comprehensive and expert assessment. As a result, you require a qualified inspector who is familiar with the rules and has enough work experience to understand what constitutes a reasonable risk.
The risk assessment, according to the HSE, consists of five fundamental elements:
- Identifying normal hazards
- Identifying individuals who might be harmed, and how they could be harmed
- Evaluating all possible risks and deciding on precautions
- Recording the findings and implementing solutions
- Reviewing and updating your assessment as warranted
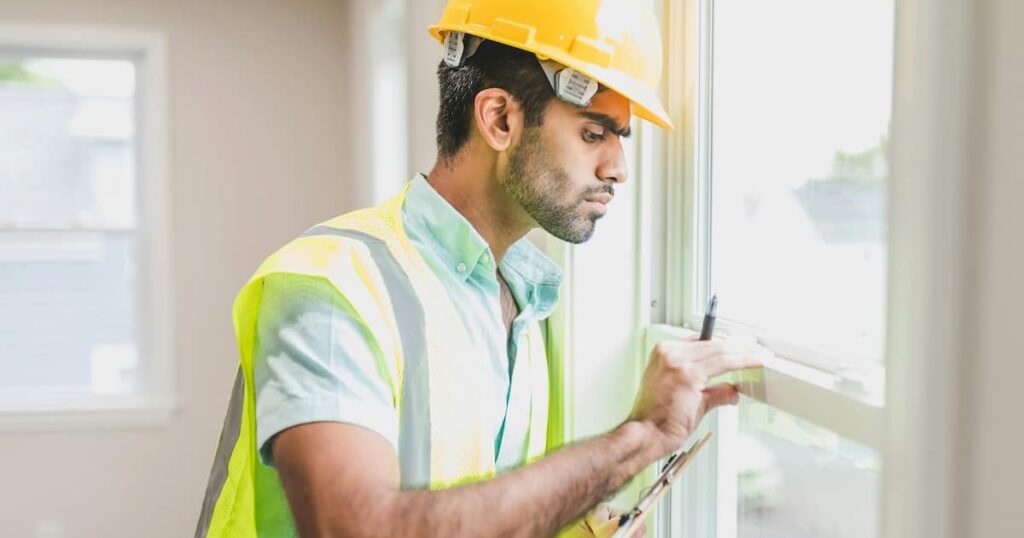
Identifying normal hazards
According to the HSE guidelines identifying normal hazards should not be complicated; neither should business owners attempt to make it more complicated than it is. In most cases you will have a good idea of what constitutes a normal hazard simply by having a few years of experience on the job. For example, you might know that workers have a tendency to leave materials and equipment too close to walkways or the leading edge. That is a normal hazard which can easily be dealt with through the implementation of certain procedures.
If you read the HSE documentation you’ll find that the term “reasonable” appears throughout. The regulations are not designed to micromanage every little thing a company does when working at height. It simply mandates that you identify normal and reasonable hazards and implement steps to mitigate risk.
Normal hazards are classified as conditions or actions, normally existing on your work site that could pose the risk of fall. There might be some other conditions that occur regularly, albeit not on a daily basis, that are also well known enough to be considered normal hazards. As long as normal hazards are identified and dealt with, the risk of injury from falls is greatly reduced. Anything not considered a normal hazard must be weighed against the likelihood that such a condition will occur, and whether or not the risk can be reasonably reduced.
How could workers be harmed?
The second portion of the risk assessment is a little more difficult because you must take into consideration the unpredictable nature of human beings. Of all the factors involved in implementing effective safety plans, human beings are the weakest link because we cannot always be depended on to do the right thing. Therefore, your risk assessment must take into consideration who is most likely to be injured at work and how that injury could occur.
Using residential window washers as an example, it is most likely that the individual workers are the only ones with any real risk of injury. Customers don’t generally stand outside and watch workers perform their tasks. Therefore, your reasonable precautions should include protecting the workers through the use of specialized working-at-height equipment that allows them to work from the ground at all times. If a home is large enough to require scaffolding, then you’ll need to also consider the possibility of individuals walking around or underneath it.
How to evaluate all possible risks and decide precautions
In addition to identifying normal hazards and the various individuals who are at risk of injury, you must also consider any additional circumstance that might raise the risk level. For instance, you should consider if it would be unsafe to set up scaffolding on a particular area of land because it is too soft in certain spots. If that’s the case, there are practical measures you can implement to reinforce the scaffolding and avoid it from sinking into the ground. This is just one example of evaluating risks and deciding on precautions.
You must find a solution to reduce each risk that your assessment reveals. This aspect of the inspection calls for innovative thinking that can be applied to different tasks. It is usually handled most effectively by someone who has industry experience and has actually performed the work. The greater the inspector’s experience, the better they will be at identifying risks that others might overlook. Paying attention to detail requires the inspector to adopt a strong point of observation.
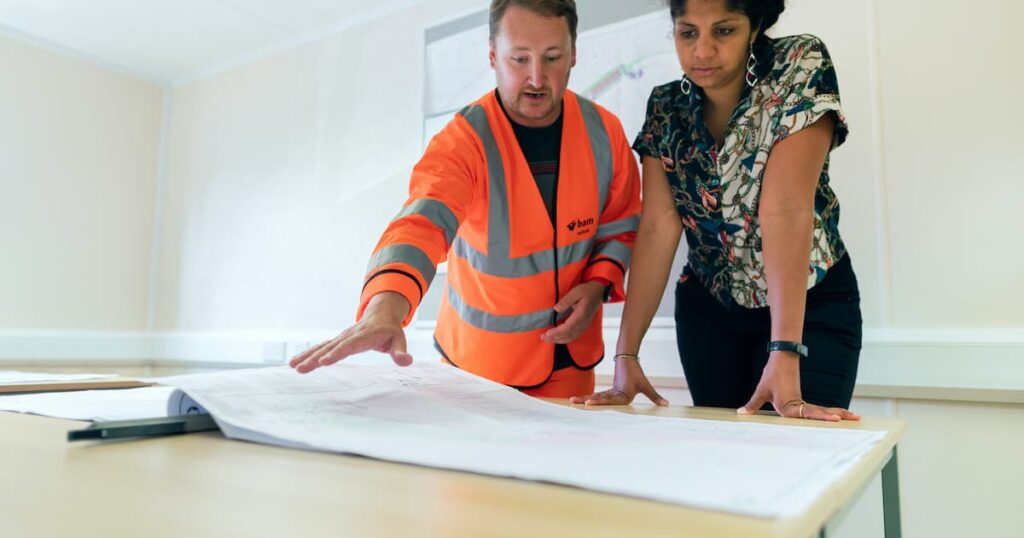
Recording your findings & implementing solutions
It’s crucial to follow the working at height regulations by recording and keeping all risk assessment results on file at the job site. This serves a couple of important purposes.
Firstly, it protects the company in case their assessment and safety practices are ever questioned in court. Having a record of who conducted the inspection, their qualifications, and the safety measures implemented is essential.
Secondly, the written record provides specific solutions to mitigate risks. A disorganised collection of potential risks and solutions can be detrimental to site safety. On the other hand, when safety assessments include concrete solutions, safety becomes more proactive and effective.
Remember, the goal of at height regulations is to ensure everyone’s safety without unnecessarily hindering productivity. The solutions you choose to implement should address the risks while still allowing workers to carry out their tasks. Learn how to examine and detect mechanical or material faults in height safety equipment in the leading edge PPE course.
Reviewing & updating your assessment
Your written assessment serves as a benchmark for future evaluations as a job site progresses. It is crucial to update the assessment regularly to account for new risks and hazards that arise during the site’s evolution.
The frequency of these updates depends on the pace of the job and how quickly new hazards emerge. Remember, updating your initial assessment doesn’t always mean making drastic changes. Sometimes, it’s just a way to reaffirm what you’ve already stated in previous evaluations.
Safety risk assessments performed properly and thoroughly lay the foundation for implementing safety practices on the job site. It is essential for your inspectors to have a deep understanding of your chosen industry and be aware of all potential risks associated with it. Without an efficient assessment conducted by a well-qualified inspector, ensuring the safety of workers becomes challenging. Managers and supervisors can learn these vital skills on the leading edge level 2 managers course.
By proactively addressing safety concerns and implementing effective measures, employers can create a healthier environment for their workforce.